From Boston University 27/05/24. Title by Superinnovators.
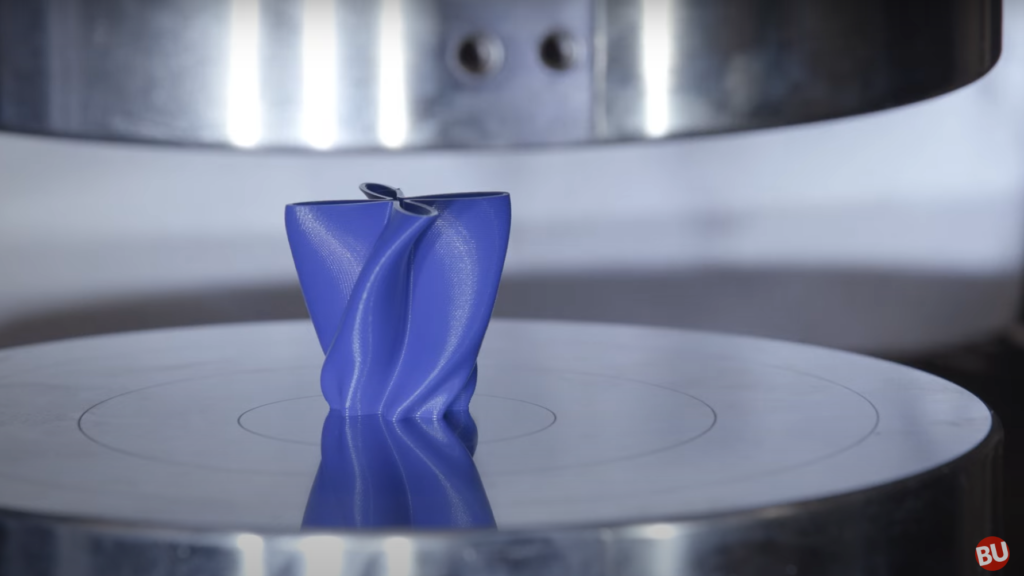
Inside a lab in Boston University’s College of Engineering, a robot arm drops small, plastic objects into a box placed perfectly on the floor to catch them as they fall.
One by one, these tiny structures—feather-light, cylindrical pieces, no bigger than an inch tall—fill the box.
Some are red, others blue, purple, green, or black.
Each object is the result of an experiment in robot autonomy.
On its own, learning as it goes, the robot is searching for, and trying to make, an object with the most efficient energy-absorbing shape to ever exist.
To do this, the robot creates a small plastic structure with a 3D printer, records its shape and size, moves it to a flat metal surface—and then crushes it with a pressure equivalent to an adult Arabian horse standing on a quarter.
The robot then measures how much energy the structure absorbed, how its shape changed after being squashed, and records every detail in a vast database.
Then, it drops the crushed object into the box and wipes the metal plate clean, ready to print and test the next piece.
It will be ever-so-slightly different from its predecessor, its design and dimensions tweaked by the robot’s computer algorithm based on all past experiments—the basis of what’s called Bayesian optimization.
Experiment after experiment, the 3D structures get better at absorbing the impact of getting crushed.
These experiments are possible because of the work of Keith Brown, an ENG associate professor of mechanical engineering, and his team in the KABlab.
The robot, named MAMA BEAR—short for its lengthy full title, Mechanics of Additively Manufactured Architectures Bayesian Experimental Autonomous Researcher—has evolved since it was first conceptualized by Brown and his lab in 2018.
By 2021, the lab had set the machine on its quest to make a shape that absorbs the most energy, a property known as its mechanical energy absorption efficiency.
This current iteration has run continuously for over three years, filling dozens of boxes with more than 25,000 3D-printed structures.
Why so many shapes?
There are countless uses for something that can efficiently absorb energy—say, cushioning for delicate electronics being shipped across the world or for knee pads and wrist guards for athletes.
“You could draw from this library of data to make better bumpers in a car, or packaging equipment, for example,” Brown says.
To work ideally, the structures have to strike the perfect balance: they can’t be so strong that they cause damage to whatever they’re supposed to protect, but should be strong enough to absorb impact.
Before MAMA BEAR, the best structure anyone ever observed was about 71 percent efficient at absorbing energy, says Brown.
But on a chilly January afternoon in 2023, Brown’s lab watched their robot hit 75 percent efficiency, breaking the known record.

The results have just been published in Nature Communications.
“When we started out, we didn’t know if there was going to be this record-breaking shape,” says Kelsey Snapp (ENG’25), a PhD student in Brown’s lab who oversees MAMA BEAR.
“Slowly but surely we kept inching up, and broke through.”
The record-breaking structure looks like nothing the researchers would have expected: it has four points, shaped like thin flower petals, and is taller and narrower than the early designs.
“We’re excited that there’s so much mechanical data here, that we’re using this to learn lessons about design more generally,” Brown says.
Their extensive data is already getting its first real-life application, helping to inform the design of new helmet padding for US Army soldiers.
Brown, Snapp, and project collaborator Emily Whiting, a BU College of Arts & Sciences associate professor of computer science, worked with the US Army and went through field testing to ensure helmets using their patent-pending padding are comfortable and provide sufficient protection from impact.
The 3D structure used for the padding is different from the record-breaking piece—with a softer center and shorter stature to help with comfort.
MAMA BEAR is not Brown’s only autonomous research robot.
His lab has other “BEAR” robots performing different tasks—like the nano BEAR, which studies the way materials behave at the molecular scale using a technology called atomic force microscopy.
Brown has also been working with Jörg Werner, an ENG assistant professor of mechanical engineering, to develop another system, known as the PANDA—short for Polymer Analysis and Discovery Array—BEAR to test thousands of thin polymer materials to find one that works best in a battery.
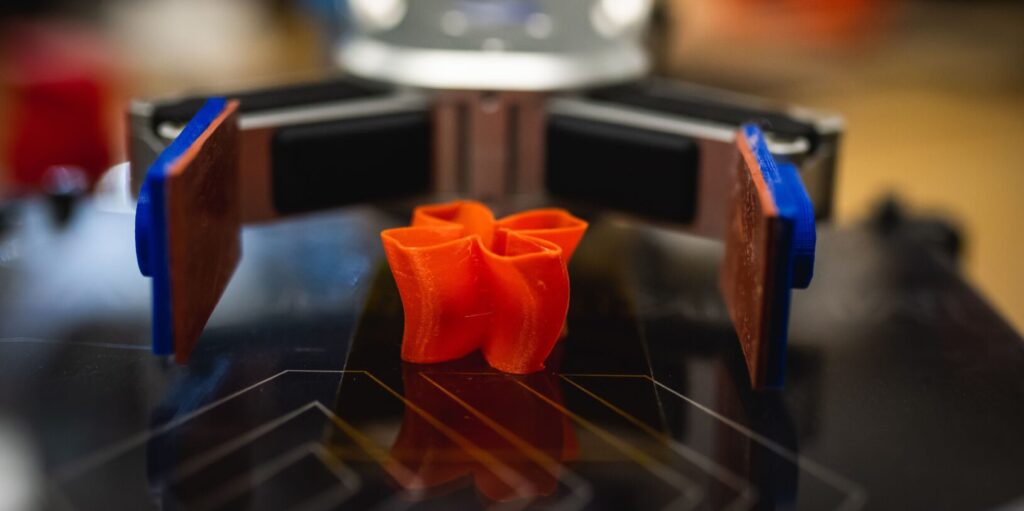
“They’re all robots that do research,” Brown says.
“The philosophy is that they’re using machine learning together with automation to help us do research much faster.”
“Not just faster,” adds Snapp.
“You can do things you couldn’t normally do.”
“We can reach a structure or goal that we wouldn’t have been able to achieve otherwise, because it would have been too expensive and time-consuming.”
He has worked closely with MAMA BEAR since the experiments began in 2021, and gave the robot its ability to see—known as machine vision—and clean its own test plate.
The KABlab is hoping to further demonstrate the importance of autonomous research.
Brown wants to keep collaborating with scientists in various fields who need to test incredibly large numbers of structures and solutions.
Even though they already broke a record, “we have no ability to know if we’ve reached the maximum efficiency,” Brown says, meaning they could possibly break it again.
So, MAMA BEAR will keep on running, pushing boundaries further, while Brown and his team see what other applications the database can be useful for.
They’re also exploring how the more than 25,000 crushed pieces can be unwound and reloaded into the 3D printers so the material can be recycled for more experiments.
“We’re going to keep studying this system, because mechanical efficiency, like so many other material properties, is only accurately measured by experiment,” Brown says, “and using self-driving labs helps us pick the best experiments and perform them as fast as possible.”